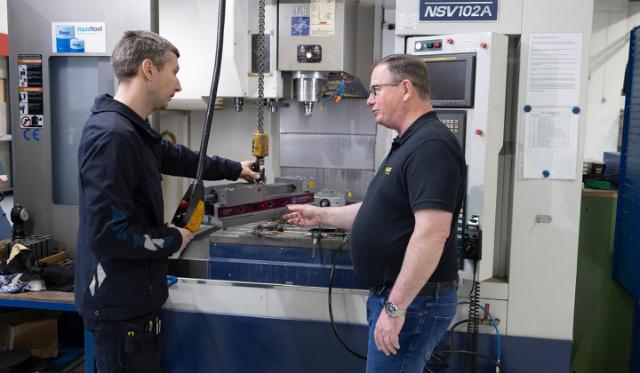
Kongskilde Industries
If you keep your momentum you can charge up pretty much all the climbs and the descents are steep and tricky.
Goodbye to time-consuming CNC milling machine conversions – increased both earnings and job satisfaction
They have optimized their setup times, which has had a noticeable impact on production efficiency.
Kongskilde are specialists in pneumatic transport and material handling solutions. The company started by making grain blowers and today can boast of making material handling systems for both grain and the paper, packaging and plastics industries.
In the fall of 2022, Kongskilde invested in a STARK SPEEDY Classic 1 zero-point clamping system through Duroc Machine Tool (DMT). This is actually the third CNC machine at Kongskilde that has been installed with a zero-point system, which has been a major turning point for how efficiently Kongskilde uses their milling machines today.
Time-consuming conversion of CNC milling machines is to blame for far too much downtime
Allan Hansen, a CNC milling operator at Kongskilde, is the man behind the idea that the newly purchased milling machine for Kongskilde’s production should be installed with a zero point system – just as two CNC milling machines had previously been very successful. One of the tasks that still requires far too much downtime in the majority of traditional productions is the conversion and setup of workpieces on milling machines, which was also the cause of a large amount of downtime at Kongskilde.
In a production with relatively small batches of workpieces – between 4 and 500 pieces – the conversion and setup of Kongskilde’s CNC milling machines took up a large percentage of the production time for Allan and the other operators. When the CNC machine needed a new setup, the machine had to stand still for a long time while it was programmed and everything was clamped manually. This approach results in an inappropriate amount of wasted time, which can be reduced to an absolute minimum with a zero-point system.
It used to be that every time I had to change the setup on my router, I had to spend a lot of time tightening, loosening, and adjusting. I had to reset every time and figure out where I was and where everything was. I wanted to avoid these kinds of trivial adjustments.
What is a zero-point system?
A zero-point clamping system is a system installed with your CNC milling machine that allows you to clamp workpieces with high accuracy, quickly and easily, and with wide flexibility using retractable clamping bolts. STARK is a world-leading manufacturer in the field, and their zero-point systems are distinguished by the fact that they can be controlled hydraulically, pneumatically, electrically, and mechanically.
The 5 best benefits of a zero-point clamping system
The 5 best benefits of a zero-point clamping system
A system such as the one Kongskilde delivered has obvious advantages for production:
- Changeover times are reduced by 50-80%
- Increased spindle times with the machine in operation
- No need for manual alignment
- Free of screws, studs and clamps
- Minimal risk of incorrect positioning of workpieces on the machine
- Extremely high precision and uniform clamping force
- The zero point of the ISO program can be set up from the CAM system
- Increased quality of workpieces
Possibility for operators with less experience to independently carry out production
Overall, these advantages provide increased productivity and incredible flexibility, as the possibility of external setup both frees up a lot of time and increases productivity from day 1. The saved setup time naturally reduces the time when the machine is out of operation, which provides a much higher efficiency in machining workpieces and the possibility of setting up pallets outside the machine, while the machine is actually running efficiently.
The zero point system is also future-proof and modular, which means that it can be used for many different tasks.
Which productions benefit from zero-point systems?
In principle, all companies with CNC machines in the plastics and metal industries will be able to optimize their production by using a zero-point clamping system for both turning and milling. However, a zero-point system is particularly advantageous in productions with relatively small batch sizes, where setup times otherwise constitute an unfavourably large percentage of the time. When changeover times are reduced to a minimum, the company earns even more on each individual part produced. In addition, the system enables very safe and ultra-precise clamping, which provides unsurpassed repeatability in productions with low tolerances and challenging parts.
The payback period for a zero-point system is between six and 12 months. From there, it generates steady profits on a daily basis.
Henrik Bach Søren, technical consultant at Duroc Machine Tool, adds:
“The zero-point system enables, among other things, external setup of tools – outside the machine – while the machine is still running. In addition, the operator can do the CAM programming himself externally on his PC and transfer it to the milling machine's application - again while the machine is still running."
STARK Speedy Classic 1 – zero point system for CNC milling machines
Kongskilde decided about 1.5 years ago to acquire another CNC milling machine for production. Allan received his new used Chiron FZ 18 L in the fall of 2022. It had barely made it through the door at Kongskilde before it had a zero-point clamping system installed. Kongskilde had already had great success twice before with the zero-point system mounted on two of the company's other CNC machines in production. That's why they were very aware of how much more efficient, easier and precise a machine with a zero-point system runs.
On the sidelines of both previous installations was DMT, which has been Kongskilde's regular partner on technical matters regarding CNC machines in production for many years. It is therefore also natural for CNC milling operator Allan Hansen that it was Henrik Bach Sørensen from DMT who was on the other end of the phone when he called to order another zero-point system on his newest milling machine.
At Kongskilde, they prioritize having a technically competent advisor in the CNC area who knows their production and company almost as well as they do, and who, through their many years of collaboration, can challenge the way they do things.
The setup just sits where it should
Allan enthusiastically talks about how easy it is now: “The changeover time has been greatly reduced. It’s so easy. Both vices and planes can be used. There are no bolts to tighten. I don’t have to do the boring work and have saved an incredible amount of time in connection with changing over the milling machine. Now I just click it off and click on a new module that I have prepared while the machine was running. And then it runs immediately. That way I have more time to make the programs, more time for optimization in production.”
In Kongskilde’s production, they change over the milling machine between 1 and 10 times a week, which has meant many hours per week that have been released for optimization work, while the machine is still running in production. This provides a much higher efficiency and uptime in production, while completely avoiding errors in connection with setting up workpieces on the machine, as the zero point system ensures that it is clamped in exactly the same place every time.
The key point for Kongskilde, however, according to Allan, is that anyone and everyone can now service the machine and set up and adjust the milling cutter. Kongskilde will also expand what they use the zero point clamping for. The smart modular system means that they can purchase new modules and use the same zero point system for multiple tasks, since STARK SPEEDY Classic belongs to a large product family with many application and accessory options.
Record-breaking setups have increased profits and job satisfaction at Kongskilde Industries
Although it has only been a few months since the zero point system was put into use onthe newest milling machine, it has already made a big difference. The most important difference being that they have said goodbye to trivial, boring setups. No more having to find new zero points every time.
Increased competitive advantages at Kongskilde
This has given Kongskilde Industries a major competitive advantage over other players in the industry on several levels. They can now produce very small batch sizes and do so profitably because it takes so little time to set up the necessary tools.
In an industry where it can be difficult to find labor, it is also positive for us that Kongskilde can now use less experienced employees to change over and maintain the machines. This makes it much easier for Kongskilde to be efficiently staffed, and it contributes to increasing employee satisfaction because they can focus on what they do best.
A milling machine that is running earns money for the company, while a stopped machine costs money. With the time saved on changeover and thus increased spindle times, Kongskilde Industries has also increased their earnings, flexibility and turnover opportunities.
The good cooperation continues…
Right now, there are no concrete projects on the drawing board between Kongskilde Industries and Duroc Machine Tool, but Allan has loose plans in mind: “On my newer used milling machine, I still have the old vices. So when they need to be replaced, I will definitely contact Henrik. They also sell these Hilma vices that we need.”
At one point in 2022, for example, Henrik was visiting Kongskilde, where Allan somewhat randomly mentions a milling machine that vibrates and shakes, to which he asks if there is a way they can avoid turning down the speed of the machine and still avoid the strong vibrations and shaking.
Long story short; The knife head that was in the spindle of the milling machine had the wrong cutting geometry in relation to the type of machining that was being done on the milling machine. Henrik ensures that the cutter head is replaced with a cutter head from BIG KAISER with the right cutting geometry for the processing that this machine performs. The new cutter head has made face milling of a surface on an unstable workpiece much, much easier and more stable. Now the cutter runs much better, and so does the result on the workpiece itself, because we avoid vibrations.
Does your production need a boost? Do you want a technically competent partner who knows how critical downtime is and who can help you meet even more ambitious goals for your production? Then Duroc Machine Tool is the one for you.
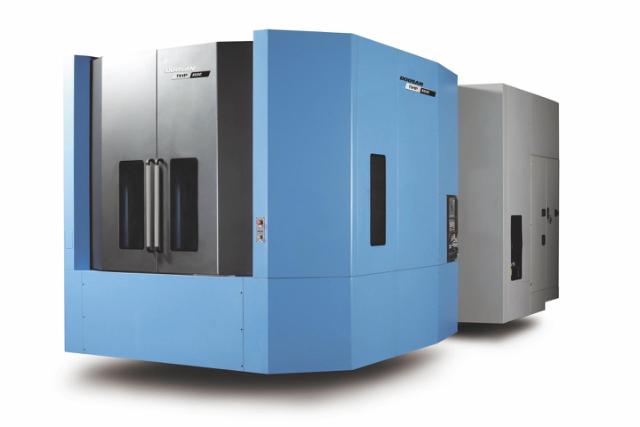
IRON Pump
IRON Pump has invested in a Doosan NHP 8000 with a pallet system to increase capacity and streamline production processes.
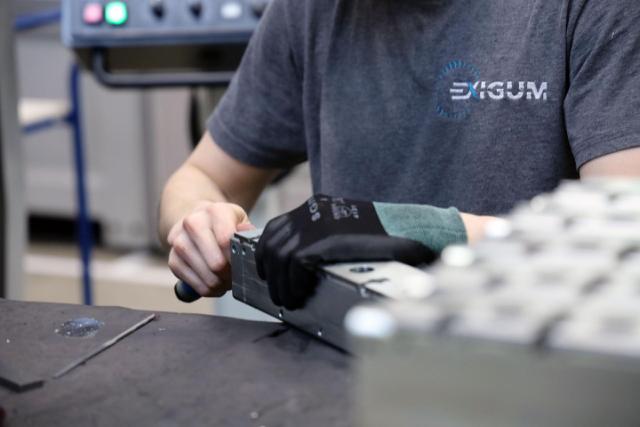
Exigum: DN Solutions is the obvious choice
Latvian Exigum has invested in seven DN Solutions (former Doosan) machines in just a few years. Exigum has chosen DN Solutions based on the total package of price, quality and customer service.
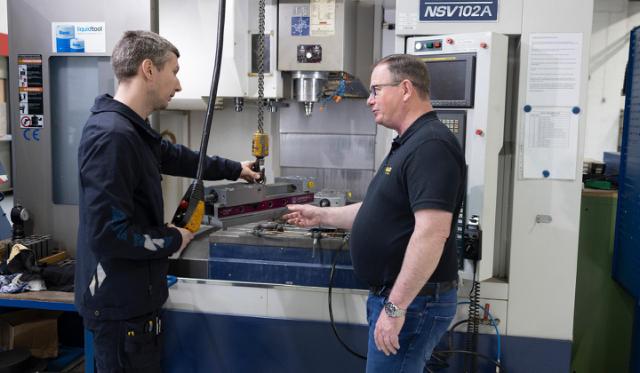
Kongskilde Industries
If you keep your momentum you can charge up pretty much all the climbs and the descents are steep and tricky.