Industrial Robot Solutions for Manufacturing
Industrial robots for CNC machines boost manufacturing with precision, versatility, and collaborative features. They ensure high accuracy, handle diverse tasks, and integrate seamlessly with CNC machines. By automating processes, these robots enhance productivity, offer flexibility for changing production needs, and cut labor costs. Their integration with CNC machines streamlines operations, and safety features contribute to a secure work environment. Operating 24/7, these robots play a vital role in modern manufacturing, elevating efficiency, precision, and safety for heightened productivity and competitiveness.
Discover more about Duroc Machine Tool's industry-leading robot solutions, known for their exceptional stability and reliability in the market.
The SYNERGi Series
Automation: know-how with the show-how
SYNERGi automated manufacturing systems take your productivity, performance and profitability to whole new levels, with their expandable design, innovative robot part loading and unloading systems and easy-to-use SYNERGi software.
The Premier and Sprint systems can be integrated easily, and seamlessly, with DN Solutions CNC lathes, machining centres and mill-turn machines - transforming their performance and bringing lights-out, unattended operation within easy reach.
If you’re looking for a state-of-the-art, Factory-of-the Future automation solution - you’ve come to the right place. And your journey has just begun.
SYNERGi Premier
Automated Manufacturing Cells - Top of the league performance
Everything about the SYNERGi Premier system has been designed with top-notch features designed to streamline your production processes. Each system includes an advanced Fanuc industrial robot, a versatile five-drawer system for seamless part loading and unloading, and a user-friendly 17” touchscreen integrated with SYNERGi software for enhanced control.
But that's not all. These cells also come with an inspection and parts ejector conveyor, an efficient air blast end-effector, precise locating plates, and flexible pneumatic 2- or 3-jaw grippers. Safety is paramount, which is why they incorporate integrated SICK safety systems, industrial robot fencing, and the option for a part turnover station to further optimize workflow.
Standard System
The standard system is ideal for all types of production i.e. from Low-Volume/High-Mix through to High-Volume/Low-Mix, and is supplied with:
- an industrial robot with a 25kg payload.
- an innovative 5 drawer part loading and unloading station.
- a 17” touchscreen HMI with a separate keyboard powered by SYNERGi software.
- a part inspection conveyor.
- industrial safety guarding.
- laser floor scanner technology.
- 2- or 3-jaw pneumatic grippers.
Options
A range of options are available for SYNERGi Premier systems that help fine-tune their performance to meet customers’ specific manufacturing requirements. These options can include:
- different multi-socket inserts that optimise the part loading/unloading capacity of a system’s grid plate, and enable components to be stacked on top of one another.
- sophisticated ultra-sonic probes for improved part height verification.
- advanced 2D and 3D vision systems essential for high-accuracy inspection and measurement, picking and placing operations etc.
- bespoke workholding, fixtures, clamping systems etc.
- part wash stations.
- additional part exit/inspection conveyor.
Customisation
SYNERGi Premier standard systems can be further customised to meet specific customer’s requirements. Customisation can include:
- the adoption of more powerful industrial robots with a higher payload.
- the reconfiguring of the standard system (i.e. the position of the loading/unloading station and robot) to best fit in with customers’floor space constraints.
- the installation of 7-axis robot rails (to allow the robot to service more than one Doosan machine).
- the integration of other technologies and processes (i.e. inspection,wash stations etc.).
SYNERGi Sprint
Getting down to business fast.
The SYNERGi Sprint system is our smallest industrial automation solution.
It is very compact and flexible, and have been designed to help customers improve the productivity of their DN Solutions machines and their manufacturing operations - reducing set up times and increasing machine tool utilisation.
Standard System
SYNERGi Sprint systems are ideal for component manufacturers machining small-to-medium batch series - the standard system features:
- an industrial robot with a 25kg payload.
- a 900mm x 900mm part loading and unloading grid plate.
- a 17” touchscreen HMI with a separate keyboard powered by SYNERGi software.
- a part repositioning stand.
- industrial safety guarding.
- laser floor scanner technology.
- 2- or 3-jaw pneumatic grippers.
Options
A range of options are available for SYNERGi Sprint systems that help fine-tune their performance to meet customers’ specific manufacturing requirements. These options can include:
- different multi-socket inserts that optimise the part loading/ unloading capacity of a system’s grid plate, and enable components to be stacked on top of one another.
- sophisticated ultra-sonic probes for improved part height verification.
- advanced 2D and 3D vision systems essential for high-accuracy inspection and measurement, picking and placing operations etc.
- bespoke workholding, fixtures, clamping systems etc.
- part wash stations.
- additional part exit/inspection conveyor.
Customisation
SYNERGi Sprint standard systems can be further customised to meet specific customer’s requirements. Customisation can include:
- the adoption of more powerful industrial robots with a higher payload.
- the reconfiguring of the standard system (i.e. the position of the loading/unloading station and robot) to best fit in with customers’floor space constraints.
- the installation of 7-axis robot rails (to allow the robot to service more than one Doosan machine).
- the integration of other technologies and processes (i.e. inspection, wash stations etc.).
Would you like to receive further information?
Feel free to reach out to us if you are interested in learning more about our automation solutions.
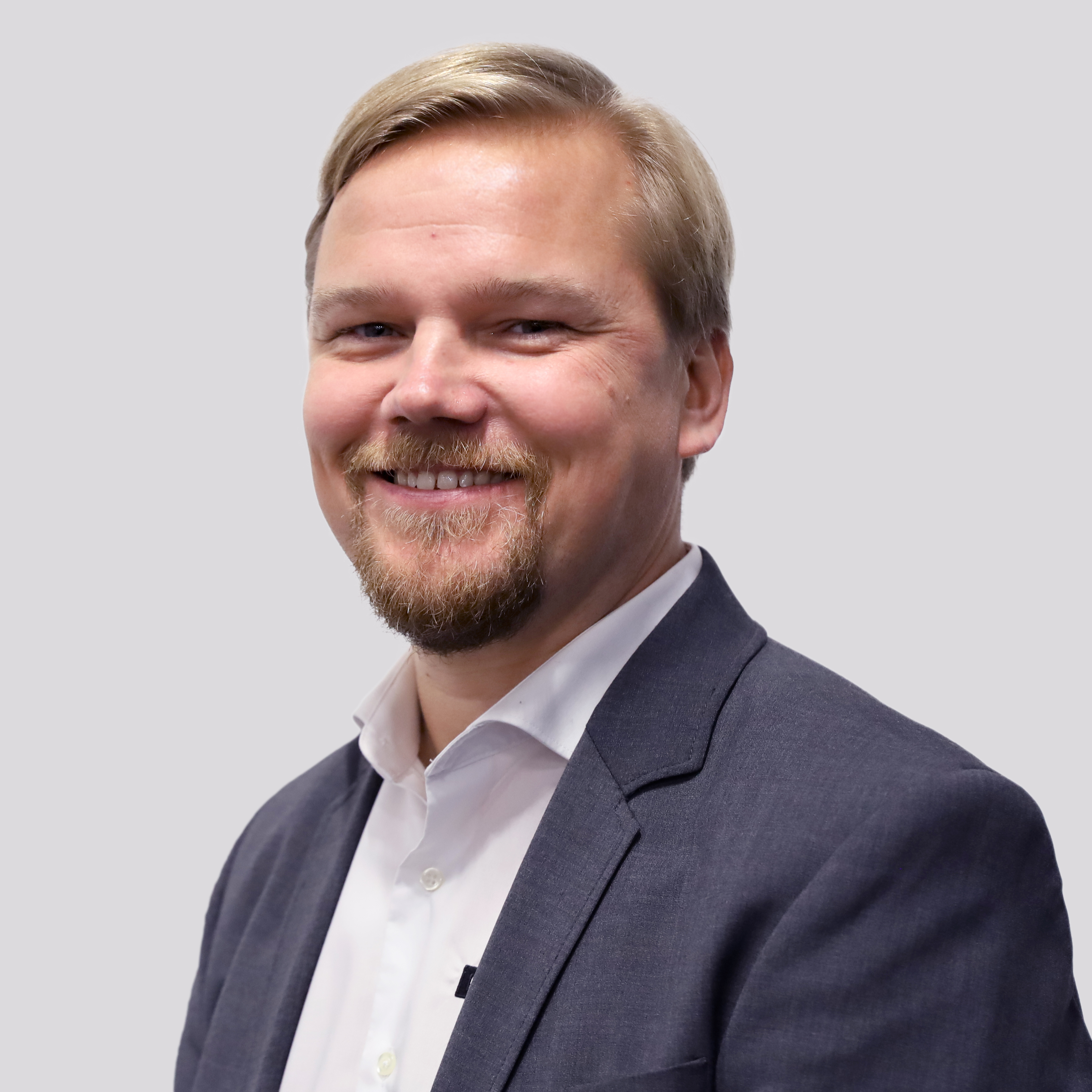