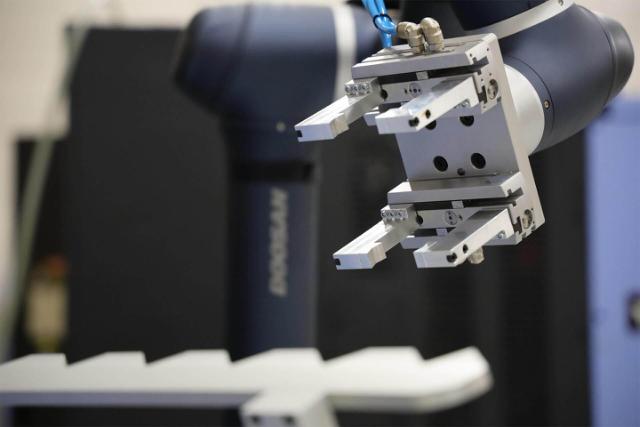
CNC milling machines with collaborative robots strengthen your competitiveness
Boost Efficiency and Stay Competitive with Robotic Automation in CNC Production
New automation processes for your CNC milling machines and lathes are designed to make your processes more efficient. They can, for example, optimise your workforce by taking over some of the most monotonous tasks, so that the employees' resources can be moved to other areas. In this way, you achieve competitive advantages in your production without necessarily having to move work processes in production to countries with lower wage costs.
At the same time, automation with, for example, cobots does not have to be an unreasonably large investment, and cobots can even be readjusted if your needs change in the future.
In this post, we go into detail about the opportunities for efficiency that robotic automation provides in your production, and what direct benefits collaborative robots provide your company and employees. We get into the process from considerations to a ready-to-run cobot, who will control the cobot and the financial parts of the decision.
What is a collaborative robot?
Collaborative robots, also called cobots, are particularly suitable for high-volume production, where high demands are placed on the overall reliability, efficiency, performance and uptime of the CNC setup.
A cobot is designed to work together with people and assist and facilitate ergonomically inconvenient and monotonous tasks –sort of an extra hand to the employee. Cobots are therefore not shielded while they work. For reasons of safety, they are therefore limited in relation to, for example, speed and strength.
On the other hand, a collaborative robot is a flexible investment that can be installed and benefit in almost any industry. They can be adapted with equipment and accessories for current and future productions.
The Versatility and Benefits of Collaborative Robots
Cobots are capable of performing tasks such as:
- Work piece processing
- Collection
- Painting
- Injection moulding
- Welding
- Packing
- Polishing
- Labelling
- Screwing tasks
Collaborative robots for automation can be used for both CNC milling machines and CNC lathes and they are, as mentioned, relevant in productions where a large number of the same workpiece is produced, which is often smaller and does not weigh a lot.
When we talk about automation on CNC milling machines, we distinguish between vertical and horizontal milling machines (or machining centres). Vertical milling machines are most often automated with a robotic arm – and in some cases with a pallet system. Horizontal milling machines are often automated with pallet systems and/or robotic solutions. Automation on (horizontal) lathes can typically be in the form of bar loaders or Gantry loaders.
Robotic automation of CNC production has many advantages - just keep reading below.
5 advantages of automating CNC milling machines and lathes with cobots
Cobots for CNC milling machines and CNC lathes are actually so efficient and affordable that they can compete with products produced in countries with much cheaper labour than we have at home. Here we go in depth with the many advantages of automating CNC milling and lathes.
The operation of a cobot is optimised for humans rather than assembly lines, unlike traditional cooperative industrial robots. This means that safety is always top-notch, which can be seen in the design of the cobots, where emphasis is placed on wires being hidden and all edges being soft. That way, fingers don't get caught, and nothing risks getting stuck.
The movement speed and safety of a collaborative robot is adapted to the human work rhythm, so any collisions with the robot will be perceived as a human touch, activate the resistance sensor and make the robot stop.
Where cooperative industrial robots require shielding, a cobot can thus work more freely and in collaboration with the human at the CNC machine. It is both highly reliable and secure.
With cobots at your CNC milling machines and lathes, you can utilise existing equipment for a much greater part of the hours of the day by letting your CNC robot take over the night shift, for example. In this way, you achieve shorter delivery times in your production to the delight of your customers.
The increased earnings, flexibility and shorter delivery time give your company great competitive advantages in the industry - without you having to outsource tasks to the East, but can keep them under your own control.
You are also not forced to hire labour – which can be difficult to find – for unsatisfactory, uniform, boring and heavy tasks, but can instead focus on saving hands.
We can put cobots into operation quickly. It only requires a bit of advance planning and preparation (about six weeks). After this, the cobot can be up and running in a few hours and help create increased earnings from day 1 as well as reduce your operating costs. The cobot can be set up with existing CNC machines and make the CNC machine able to run 50-60% more of the hours of the day – for example also at night.
With the increased efficiency and the saved operating costs, you can also achieve a short payback period of less than 1 year when you invest in a cobot.
It benefits the working environment and improves the well-being of your employees when work tasks that are physically demanding and very monotonous are taken over by a machine, so that the operator is not physically overloaded by ergonomically poor work movements.
The operator, on the other hand, can focus on the more complicated and varied tasks, which are experienced as creating more value for him/her.
It actively contributes to reducing the number of sick days and minimises the risk of occupational injuries.
Here it is important to mention that successful automation always starts from the operator's professional knowledge and skills. The cobot must not be seen as a replacement for the person in question, but as an assistance that takes over tasks and functions, to the benefit of the economy and the operator in question.
From Planning to Ready-to-Run Production with Cobots
It is difficult to estimate how long a plant manager or operator might walk around their production floor, pondering if there could be a smarter, more efficient, and cost-effective way to handle the simplest and most monotonous tasks, until they finally contact Duroc Machine Tool and decide to invest in a collaborative robot.
Once you reach out to us, you will quickly receive a proposal for a potential automation solution. After the agreement is signed, there is a six-week period for preparation and equipment ordering, including the robotic arm. The actual setup takes only a few days, followed by a few days of training. The machine is then programmed and ready to run, bringing value to your production.
Who will control the automated CNC milling machine and lathe?
It is usually the operator that has the best understanding of where and how a collaborative robot can be most beneficial. Operators are familiar with all the sub-processes of the work, and they know which tasks a robot can take over.
The most effective approach is to automate the cheapest and most monotonous tasks, especially those that are not ergonomically friendly, particularly when dealing with thousands of items. This allows operators to focus on the more demanding and complex tasks that are costly to automate. In many cases, this can save up to 80% of the cost compared to automating everything.
It is crucial to involve the operator who will be working closely with the cobot once it is operational. This is often someone already on your team, so you do not need to hire new staff for these tasks, which can be challenging to fill.
When a cobot takes over part of the work process, the operator can often manage multiple automated CNC milling machines and CNC lathes simultaneously. The cell setup they oversee can ensure that items are washed, dried, and even packed if necessary. If the operator needs to step away, there are no consequences for spindle times, as the cobot continues to operate seamlessly.
Financing – Fast Repayment
Many companies mistakenly believe that collaborative robots require a significant and complicated investment with a long payback period, similar to their experience with industrial robots.
This misconception often leads companies to purchase and set up the collaborative robots themselves, which can be time-consuming. There have been cases where companies did not achieve full operational status until 14 months after installation.
However, the payback period for a collaborative robot is typically less than a year. As mentioned earlier, a cobot can increase the utilization of existing equipment by 50-60%, allowing a CNC machine to run up to 80 hours a week — far more than human operators can achieve, typically covering four hours during the day and six hours at night.
By consulting with Duroc Machine Tool, you can quickly get started with your collaborative robot. With its short payback period, the cobot we set up will begin enhancing the productivity of your CNC milling machines and lathes within eight weeks. After a year, it will be generating profit daily. Professional advice in the setup process is highly beneficial, especially as it requires consistent production of the same items in large quantities to be most effective.
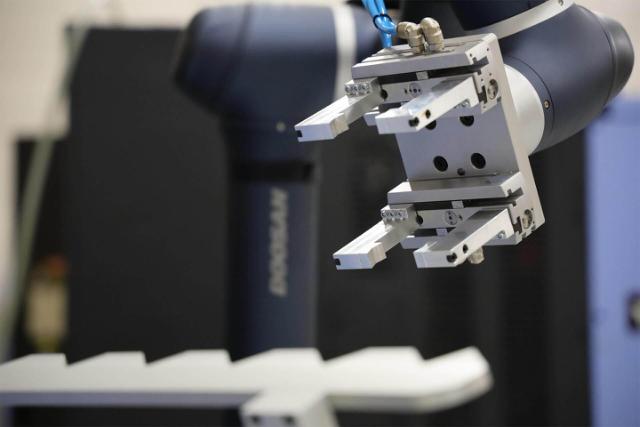
CNC milling machines with collaborative robots strengthen your competitiveness
Do you often solve tasks in the same way either because it works or maybe because that's the way you've always done it?